|
 |
|
The following page was printed from RemoteCentral.com:
Topic: | Central Vac in poured concrete walls This thread has 54 replies. Displaying posts 16 through 30. |
|
Post 16 made on Wednesday July 18, 2018 at 08:14 |
highfigh Loyal Member |
Joined: Posts: | September 2004 8,322 |
|
|
On July 17, 2018 at 23:46, SB Smarthomes said...
You're correct that the homeowner won't be the one vacuuming, but they have central vacs in other homes and want it in this house too. They are so assertive about having central vac everywhere that I'm installing a second power unit for the cabana with a single inlet so they have central vac in that area too. Were those other homes built the same way or did they have stud walls and furring over concrete?
|
My mechanic told me, "I couldn't repair your brakes, so I made your horn louder." |
|
Post 17 made on Wednesday July 18, 2018 at 08:43 |
cshepard Advanced Member |
Joined: Posts: | June 2008 767 |
|
|
At least you’re not doing Hide-A-Hose....
|
Chris |
|
Post 18 made on Wednesday July 18, 2018 at 09:07 |
diesel Senior Member |
Joined: Posts: | April 2004 1,177 |
|
|
One thing you may have to consider too is issues that may arise putting a 3" pipe in an outside wall that is 8" thick. I used to pour basement foundations and NEVER (at least in my area) did I see plumbing vertical in an outside wall. Will this cause an engineering issue (i.e. - load) and if so you would now be liable for foundation cracks, leaks, or worse. I could be off, but check with local foundation companies to see if they know if this is acceptable or even common practice and see if there is a procedure you would need to follow.
Also you will need to plan on being there as they install the forms because that can happen very quickly and chances are they won't stop and wait for you. Not sure how you are going to seal the end of your pipe to the form either, I don't envy you on this one!
|
|
OP | Post 19 made on Wednesday July 18, 2018 at 10:59 |
SB Smarthomes Super Member |
Joined: Posts: | July 2007 2,634 |
|
|
On July 18, 2018 at 00:31, Ernie Gilman said...
Rust. How many years is this good for?
The metal vac pipe is also available in stainless steel, but when I spoke to the supplier some time ago they recommended against using any type of metal pipe for this application so looks like it will be some type of PVC.Unless the concrete pour crushes it, then you won't be able to use it.
Small diameter smurf (1/2") is quite rigid and won't be crushed. The vac pipe and low volt conduit won't be in the slab itself but will down below it in what is usually compacted sand. I"ll probably go ahead and pull the wire through the conduit at rough in so it's already in place. Do what you're good at. You're asking for basic information and you're hoping it will work. This is NOT a predictor of success. Tell the contractor you're not good enough with central vac to do this particular house and you -- or better yet he -- needs to find someone who will do it.
If he locates companies that won't do it, that should strengthen your position that it IS A BIG DAMN DEAL that can go very badly. Don't do it yourself. Dang Ernie, thanks for the lack of confidence... figuring out hard to do stuff that no one else can or wants to do is what I'm good at. The architect, builder & clients are all aware that I've never done this before. The builder and architect both have confidence in me from past work and wanted me to be the one to do this. The builder and every trade involved are all doing something they've never done before on this job. It's very complex and highly engineered... over two years in planning and design and will be 3+ years in construction. The plan set exceeds 300 pages right now.
|
www.sbsmarthomes.comSanta Barbara Smarthomes |
|
OP | Post 20 made on Wednesday July 18, 2018 at 11:03 |
SB Smarthomes Super Member |
Joined: Posts: | July 2007 2,634 |
|
|
On July 18, 2018 at 06:15, thecapnredfish said...
Someone mentioned getting around mesh and rebar. Only outside forms go first. Then plumbing goes In as plumber puts in the pipes before rebar and mesh. Sealing ends of pipes. Plumbers cap it with PVC caps then cut them off. You are not doing anything different other than moving dust and hair instead of water and poop. Poured walls? I assume you need perfect placement. Perhaps you can build a small form around where your intake vents go to to keep cement out and give you some room to trim pipe. I’m not a vacuum guy, just going off what I see walking through houses. Crush won’t happen. The soil should be compacted. The cement does not compact the soil further, at least noticeable. Little bit down you dig will not pose an issue. Plumber does it everyday. Your vertical runs will not have weight on them anyways. If worried about under slab runs, put it in schedule 40 or use schedule 40. I'm familiar with working in forms for footings and even poured walls, it's just the first time where the form and concrete are the finish surface. In this case, it's usually the inside form that's being installed first because the electrical contractor and I need to set all our boxes to the back of the inside form which will become the interior wall surface.Yes, the wall are poured so everything has to be set and fixed onto the forms within about 1/8" accuracy and there cant be any damage to the inside of the form surface (even pencil marks show up in the concrete). Miss drilling a hole or scratching the form surface would require the concrete guys to replace the entire section of form board. I think schedule 40 is the way to proceed and then use the central pipe adapters to reduce near the inlets. I'm still not quite sure how to pull off the inlets that are located in concrete walls. Building any type of box around them would create an opening around the inlet too large for the inlet cover to conceal. Might need to fab up some steel boxes.
The good thing is there are lots of pours scheduled and I have the time and budget to create mock-ups that can be test poured to see what happens.
I was just hoping that someone had already done this so I could draw from their experience.
Last edited by SB Smarthomes on July 18, 2018 11:22.
|
www.sbsmarthomes.comSanta Barbara Smarthomes |
|
OP | Post 21 made on Wednesday July 18, 2018 at 11:23 |
SB Smarthomes Super Member |
Joined: Posts: | July 2007 2,634 |
|
|
On July 18, 2018 at 08:14, highfigh said...
Were those other homes built the same way or did they have stud walls and furring over concrete? I think they own 4-5 other homes, but they are all more traditional construction. This home is replacing another vacation home here in Santa Barbara that they completed in 2011. It has some concrete features, but this will be the first all concrete home they've built. It will be unique even by southern CA standards. To provide some context for the fit and finish required on this project, the other vacation home they have in Santa Barbara is for sale. If you want to do the math, it's over 8k sq ft and priced just under $5000 sq ft.
Last edited by SB Smarthomes on July 18, 2018 11:32.
|
www.sbsmarthomes.comSanta Barbara Smarthomes |
|
OP | Post 22 made on Wednesday July 18, 2018 at 11:52 |
SB Smarthomes Super Member |
Joined: Posts: | July 2007 2,634 |
|
|
On July 18, 2018 at 09:07, diesel said...
One thing you may have to consider too is issues that may arise putting a 3" pipe in an outside wall that is 8" thick. I used to pour basement foundations and NEVER (at least in my area) did I see plumbing vertical in an outside wall. Will this cause an engineering issue (i.e. - load) and if so you would now be liable for foundation cracks, leaks, or worse. I could be off, but check with local foundation companies to see if they know if this is acceptable or even common practice and see if there is a procedure you would need to follow.
The walls are 12" thick (5" concrete, 2" insulation, 5" concrete), but there are specifications on what's allowable inside the walls and it differs by location. The builder is great and very involved with all the trades to make sure everything is done properly... I think I mentioned in a previous post the plan set is very detailed and over 300 pages so lots to remember. Also you will need to plan on being there as they install the forms because that can happen very quickly and chances are they won't stop and wait for you. Not sure how you are going to seal the end of your pipe to the form either, I don't envy you on this one! Yes, concrete work has already been going on at this job for 6-8 months so I've already roughed in a bunch of pipe for the basement mechanical room which was the first part of the actual structure to be poured. You're also correct that scheduling is a big issue and coordinating with the concrete contractor has to be done. Aside from the central vac I've got all the low volt wiring plus Lutron HWQS, HVAC control, shades, A/V, surveillance, networking, etc and everything is in conduit. When the house is complete, there won't be any accessible attic or crawl space. Here's a few photos of the basement mechanical room: 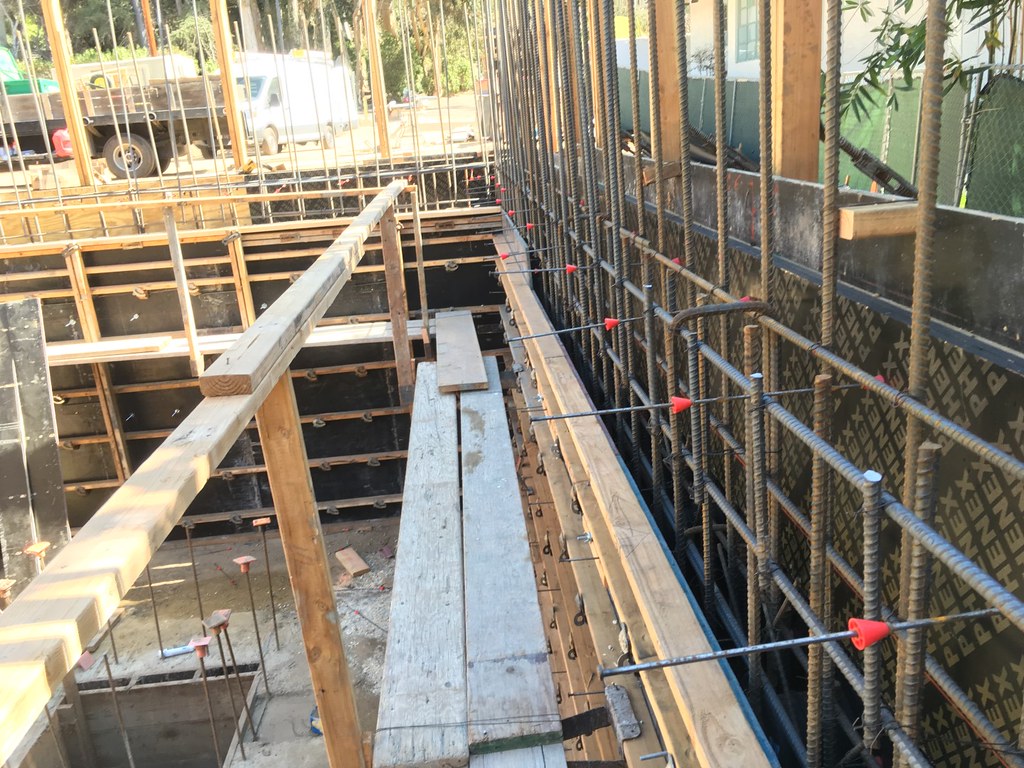 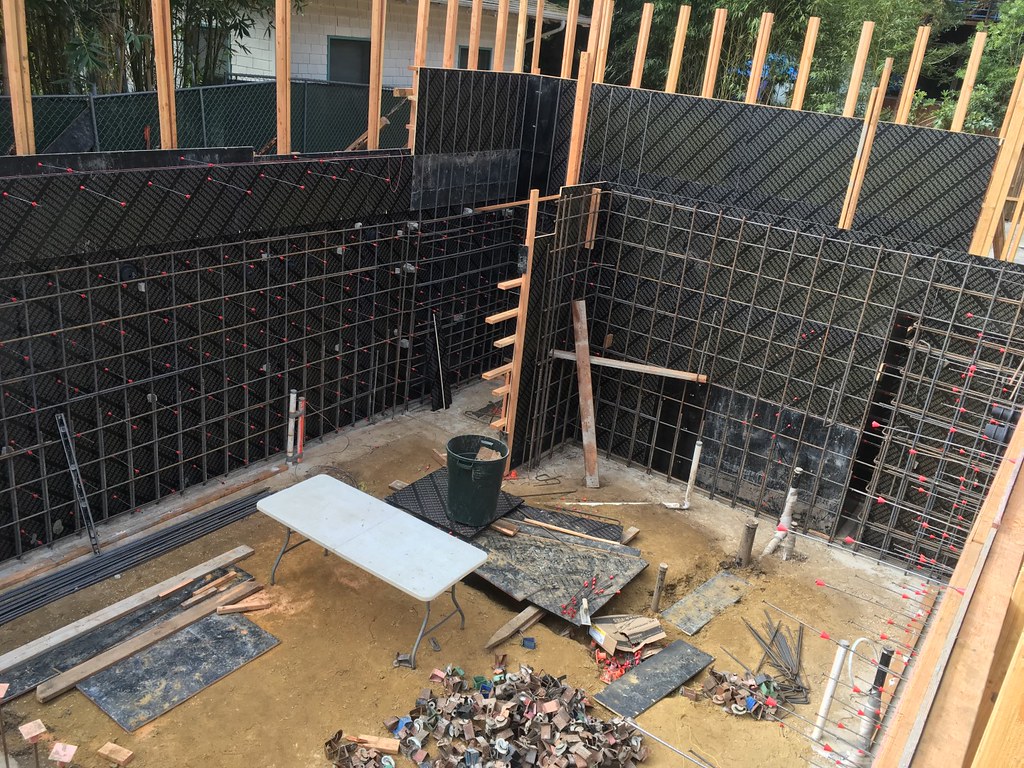 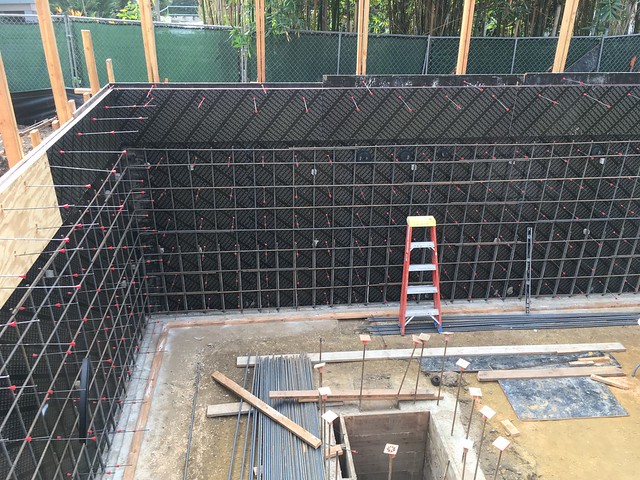
|
www.sbsmarthomes.comSanta Barbara Smarthomes |
|
Post 23 made on Wednesday July 18, 2018 at 11:58 |
Ernie Gilman Yes, That Ernie! |
Joined: Posts: | December 2001 30,104 |
|
|
On July 18, 2018 at 10:59, SB Smarthomes said...
The metal vac pipe is also available in stainless steel, but when I spoke to the supplier some time ago they recommended against using any type of metal pipe for this application so looks like it will be some type of PVC. In other words, what seems to us to be the best idea is shot down by the supplier. This might be used as a reference point for other ideas we have as to how to do this. Small diameter smurf (1/2") is quite rigid and won't be crushed. I think you're right about that, plus you say that won't be in the pour: The vac pipe and low volt conduit won't be in the slab itself but will down below it in what is usually compacted sand. I"ll probably go ahead and pull the wire through the conduit at rough in so it's already in place. Dang Ernie, thanks for the lack of confidence... This is not a lack of confidence. This is noting that several ideas have been shot down by others who should know; or others who do this for a living don't know how to do it; or (as it seems) the general contractor knows someone who says they can do it but he doesn't trust them to get it right.
|
A good answer is easier with a clear question giving the make and model of everything. "The biggest problem in communication is the illusion that it has taken place." -- G. “Bernie” Shaw |
|
OP | Post 24 made on Wednesday July 18, 2018 at 12:14 |
SB Smarthomes Super Member |
Joined: Posts: | July 2007 2,634 |
|
|
On July 18, 2018 at 11:58, Ernie Gilman said...
This is not a lack of confidence. This is noting that several ideas have been shot down by others who should know; or others who do this for a living don't know how to do it; or (as it seems) the general contractor knows someone who says they can do it but he doesn't trust them to get it right. I think the biggest issue is just the unique construction. Building with concrete is not very common in the US, so no one knows how to do it. Building with concrete is very common in many other parts of the world, but they generally aren't trying to produce a finish quality surface with it and probably aren't dealing with things like central vac, shade pockets, etc.
|
www.sbsmarthomes.comSanta Barbara Smarthomes |
|
Post 25 made on Wednesday July 18, 2018 at 12:17 |
Trunk-Slammer -Supreme Loyal Member |
Joined: Posts: | November 2003 7,462 |
|
|
On July 18, 2018 at 11:03, SB Smarthomes said...
Building any type of box around them would create an opening around the inlet too large for the inlet cover to conceal. Worst case, you can use the oversize inlet trims. I had one builder that wanted them on every CV job. His sloppy sheetrock guys created the need, and the builder actually liked the way they looked. I also like the schedule 40 adapter idea. Those were not around back in the day.
|
|
Post 26 made on Wednesday July 18, 2018 at 13:34 |
SWOInstaller Select Member |
Joined: Posts: | October 2010 1,596 |
|
|
I'm not sure how you guys do vacs in the states but we use these for all our cvac rough-ins [Link: broan.ca]SB, a couple options: 1. I would cut the wall mount portion off the above plate and get exact measurements of the unit and cut that out using plywood (ensuring the plywood is the proper depth of the bracket). Place a coupler on the end of your pipe (Don't Glue it on) and cut a hole in the plywood the diameter of the coupler. Secure the plywood to the form drilling through the plywood first. then place your pipe into the hole you cutout. Once the concrete has been poured and the forms removed you will be able to slide that bracket onto the pipe and then secure the inlet cover onto the bracket. This is providing you are wanting a cover plate sitting flat against the concrete. 2. If wanting the face of the cover plate to be flush with the face of the concrete, you will have to do the same as above, however cutting out the plywood to be the size of the inlet plate. You will most likely also have to make the depth of recess in the concrete deeper to allow for the pre-construction bracket and cover plate. Additionally you could screw option 1 to option 2 and that will get your final depth. You don't have to worry about the form being "damaged" as the cover plate will hide any imperfections in the concrete in this area. Also you could as the company doing the concrete if they have an old form you could use to cut up that would allow for a cleaner finish. The concrete company just has to ensure that they aren't sparingly with the oil on your plywood to ensure it doesn't stick to the concrete and leave pieces of wood.
|
You can't fix stupid |
|
Post 27 made on Wednesday July 18, 2018 at 13:53 |
BizarroTerl Active Member |
Joined: Posts: | October 2002 591 |
|
|
Why not just use schedule 80 PVC for the vacuum piping? Use the sweep ells and the adapters at the ends.
|
|
Post 28 made on Wednesday July 18, 2018 at 16:34 |
Craig Aguiar-Winter Senior Member |
Joined: Posts: | September 2002 1,489 |
|
|
On July 18, 2018 at 11:03, SB Smarthomes said...
.Building any type of box around them would create an opening around the inlet too large for the inlet cover to conceal. Might need to fab up some steel boxes.
The good thing is there are lots of pours scheduled and I have the time and budget to create mock-ups that can be test poured to see what happens.
Could you make a small plywood box that’s the same size as the box would be that you will insert after? Lightly glued together. Small enough in the outside dimensions that the plate will cover it. Glue it to the form. Make a hole in the back or bottom of it for the pipe to enter with a friction fit. After the form comes off it can be broken out of the concrete. Leaving the appropriate sized recess for you to plate over ?
|
My wife says I can't do sarcasm. She says I just sound like an a$$hole. |
|
Post 29 made on Wednesday July 18, 2018 at 17:17 |
diesel Senior Member |
Joined: Posts: | April 2004 1,177 |
|
|
On July 18, 2018 at 11:52, SB Smarthomes said...
The walls are 12" thick (5" concrete, 2" insulation, 5" concrete), but there are specifications on what's allowable inside the walls and it differs by location. The builder is great and very involved with all the trades to make sure everything is done properly... I think I mentioned in a previous post the plan set is very detailed and over 300 pages so lots to remember. Yeah, we don't build them like that in my neck of the woods! Everything we do around here is typically 8" thick concrete and the only time conduit touches it is when it passes through it inside to outside! That looks like lots of fun...
|
|
Post 30 made on Thursday July 19, 2018 at 08:16 |
highfigh Loyal Member |
Joined: Posts: | September 2004 8,322 |
|
|
On July 18, 2018 at 11:23, SB Smarthomes said...
I think they own 4-5 other homes, but they are all more traditional construction. This home is replacing another vacation home here in Santa Barbara that they completed in 2011. It has some concrete features, but this will be the first all concrete home they've built. It will be unique even by southern CA standards.
To provide some context for the fit and finish required on this project, the other vacation home they have in Santa Barbara is for sale. If you want to do the math, it's over 8k sq ft and priced just under $5000 sq ft. That's about what I figured- they need someone to explain the reasons why this is a bad idea or, because concrete can damage metal, it's going to take time to find the correct solution. However, if the area where a vertical pipe needs to me installed vertically, it's possible to do that without causing a structural failure IF the outside of the wall won't be visible- they can make a bump out in the wall- when it's on the inside and used to make the wall stronger, it's called a 'pilaster' and it can be reinforced with rebar or a mesh cage. That said, I don't know if that would fly in CA, with its design codes regarding earthquakes.
|
My mechanic told me, "I couldn't repair your brakes, so I made your horn louder." |
|
 |
Before you can reply to a message... |
You must first register for a Remote Central user account - it's fast and free! Or, if you already have an account, please login now. |
Please read the following: Unsolicited commercial advertisements are absolutely not permitted on this forum. Other private buy & sell messages should be posted to our Marketplace. For information on how to advertise your service or product click here. Remote Central reserves the right to remove or modify any post that is deemed inappropriate.
|
|